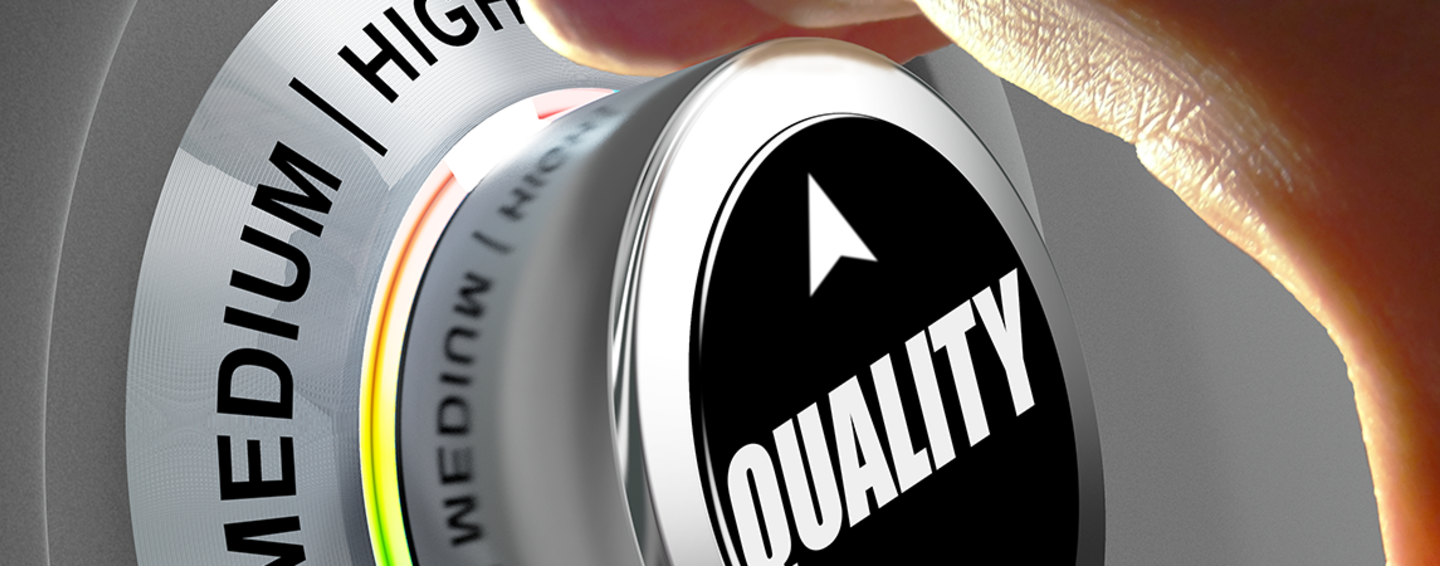
Error Proofing
Detecting and repairing defects early in production can save your business time and money. Learn how Panasonic qualifiers can help improve quality control on your assembly line.
What is error proofing?
Error proofing in a manufacturing environment refers to the implementation of fail-safe mechanisms to prevent a process from producing defects by detecting, correcting, and eliminating human error. Error proofing your assembly line is essential for effective quality control, reducing redundancies and repairs, and improved plant safety.The cost of not error proofing
Detecting and repairing manufacturing defects early in the production process can save your business money and lost production time. More importantly, you’ll protect your hard-earned reputation from long-term brand damage by minimizing product recalls, customer complaints and potential lawsuits. A well-planned error proofing system pays big dividends.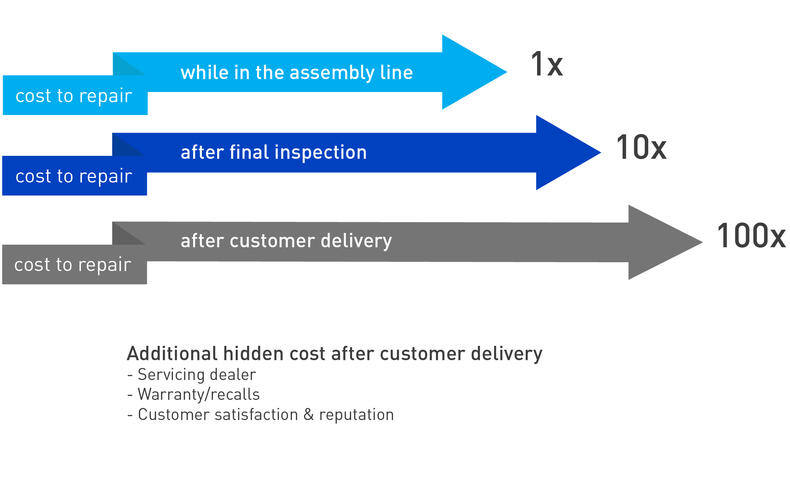
Qualifiers & error proofing
It’s easier than you think to exercise continuous improvement and quality control through error-proofing. Panasonic’s complete line of qualifiers are loaded with valuable features and are designed for easy wireless communication with our assembly tools. Our versatile qualifiers help you implement an advanced error-proofing system and a zero-defects approach, improving productivity and manufacturing quality on your assembly lines.
By combining wireless communication with a range of quality-improving functions and features, Panasonic qualifiers and cordless tools are key to high-level error proofing and production efficiency across your plants.
Quality control through error-proof fastening
- Advanced error proofing with multiple Panasonic wireless programmable tools
- Error proofing | Poka-yoke
- Assure product quality with proof through intelligent real-time data
- Simple tool connection with auto learn
- Single-tool, multi-tool and multi-workstation flexibility
Reasons to consider error proofing
-
Business
- Design best practices
- Quality control
- Consequences of not error proofing are costly and dangerous
-
Operator/machine
- Incorrect tool
- Missed fastener
- Operator error
- Inaccuracy
- Mechanical failure
-
Method
- Improper tightening
- Wrong specification
- Wrong procedure
- Wrong tool selection
-
Materials
- Improper materials
- Out of tolerance
- Defective materials
- Insufficient lubricant
Related Content
-
About Panasonic Assembly Tools
-
Features and Benefits
-
Digitized Manufacturing