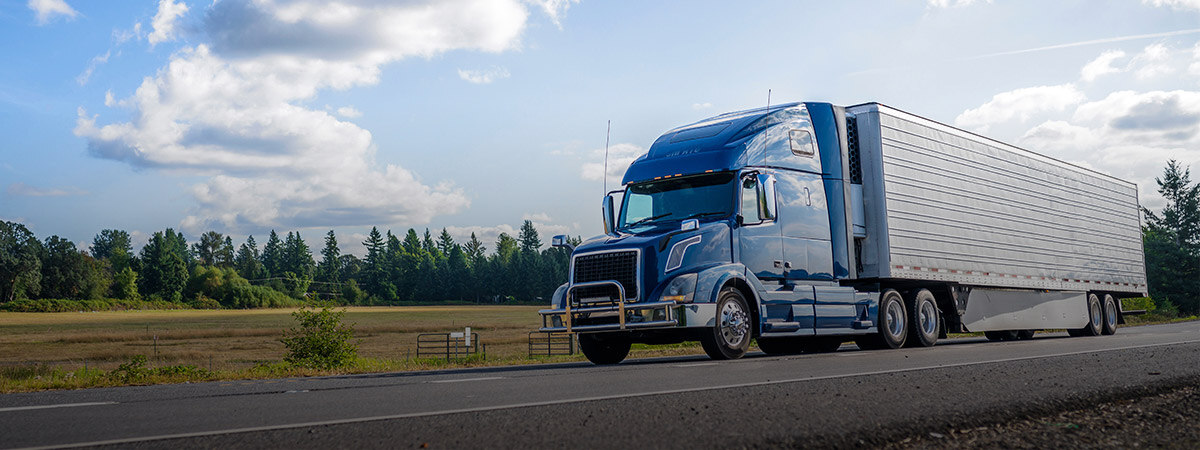
COVID-19 Vaccines Deserve VIP Treatment from the Cold Chain
The distribution of COVID-19 vaccines is today’s greatest logistical challenge. In the race to achieve herd immunity, industry players are being called on to deliver innovative technology solutions that will get us across the finish line as soon as possible.
When COVID-19 triggered a global pandemic, medical researchers rose to the occasion, developing several highly effective vaccines in just a few months. With vaccines now approved for use in Canada, the baton has passed from the research community into the hands of cold chain logistics companies, who we’re all relying on now to distribute millions of heat-sensitive doses to vaccination sites throughout the country.
Vaccine transport and storage
Although Canadians have a lot of experience managing temperature-controlled supply chains for fresh produce, seafood, frozen food, pharmaceutical products and temperature-sensitive chemicals, the current COVID-19 vaccines have unique requirements. The Pfizer-BioNTech vaccine is particularly difficult to handle because it must be maintained at -70°C or it will quickly expire. The Moderna vaccine, on the other hand, is stable at a relatively balmy -20°C, allowing cold chain companies to readily adapt some of their existing equipment to transport and store these doses.
Manufacturers typically ship the vaccines in specially constructed cold boxes. Each insulated box is packed with dry ice, which must be periodically replaced to maintain the desired low temperature range until the doses are either used or transferred to a refrigerated storage facility at a major hospital, pharmaceutical company or laboratory. When mass vaccinations get underway, doses will be sent out from the main storage facilities to vaccination sites such as clinics, pharmacies and small rural hospitals, which may not have adequate cold storage equipment.
Refrigeration OEMs worldwide are making a special effort to design more energy-efficient cold boxes that will minimize vaccine spoilage during transport. Whenever dry ice is replaced in a cold box or doses are transferred to/from a freezer, there is always a potential for harmful temperature fluctuations. A more efficient cold box would not have to be opened as frequently to maintain the contents, reducing the risk of spoilage and providing more time-flexibility for frontline medical professionals at vaccination sites with limited cold storage capacity.
Of course, any innovative vaccine handling solutions developed by refrigeration OEMs can also be applied to the rest of the cold chain, increasing the productivity and profitability of medical supply and food transport operations. Grocery stores, restaurants, their customers and the economy as a whole would certainly benefit from extended product shelf life, less food wastage and fewer cases of food-borne illness. Even a slight improvement in the energy efficiency of refrigerated transport and storage equipment could add up to a significant cost savings for companies in the food industry.
Effective thermal insulation
For refrigeration OEMs trying to build a better cold box or freezer system, the low hanging fruit on the improvement tree is— thanks to technology innovations in this field—thermal insulation. It’s no secret that the key to reducing heat transfer through the walls of a cold box is to increase the R-value of the insulation. With traditional foam insulating materials, this would mean thicker walls, resulting in either a bigger box or less storage space. However, using vacuum insulation panels, product designers can simultaneously achieve higher R-values and thinner walls.

What are vacuum insulation panels?
A vacuum insulation panel (VIP) is constructed by vacuum-sealing a porous filler material inside an impermeable metallic envelope. Since heat cannot travel through a vacuum by conduction or convection, VIPs have higher R-values than conventional insulating products for a given thickness. The insulation’s R-value can be easily multiplied by simply stacking individual VIPs together. To protect the integrity of the envelope and maintain the insulating vacuum within, workers must follow some basic installation procedures during product assembly.
VIP solutions from Panasonic
Panasonic has been manufacturing vacuum insulation panels since 1998, for use in our own products and those of our valued customers. Rated at a stunning R-63/inch, with an ultra-low thermal conductivity of 0.002 W/mK, Panasonic’s proprietary U-Vacua™ panels are the best in the industry—as much as 20 times more efficient than standard foam insulation.
Our thin, lightweight VIPs can help you ship more product with less container, while minimizing dry ice or electricity consumption. Made with 75% recycled materials, Panasonic VIPs come in a variety of standard panel sizes, plus we can produce customized panels according to your size, R-value and product life requirements. Off the shelf, U-Vacua panels already feature a long life cycle, maintaining their R-value for 10+ years, so the insulation will be effective throughout the service life of your refrigeration equipment.